Weltweit gibt es drei Arten von Flachglas: Flachziehen, Floatglas und Kalandrieren. Floatglas macht derzeit über 90 % der gesamten Glasproduktion aus und ist der Grundbaustoff für Architekturglas weltweit. Das Floatglas-Herstellungsverfahren wurde 1952 eingeführt und setzte weltweit Maßstäbe für hochwertige Glasproduktion. Der Floatglas-Prozess umfasst fünf Hauptschritte:
● Zutaten
● Schmelzen
● Formen und Beschichten
● Glühen
● Schneiden und Verpacken
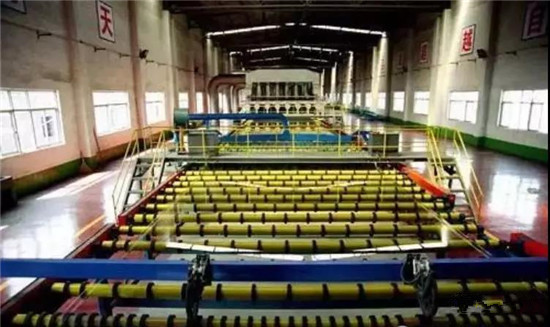
Zutaten
Die Chargenbereitung ist der erste Schritt, in dem die Rohstoffe für das Schmelzen vorbereitet werden. Zu den Rohstoffen gehören Sand, Dolomit, Kalkstein, Soda und Mirabilit, die per LKW oder Bahn transportiert werden. Diese Rohstoffe werden im Chargenraum gelagert. Im Materialraum befinden sich Silos, Trichter, Förderbänder, Rutschen, Staubabscheider und die notwendigen Steuerungssysteme, die den Transport der Rohstoffe und die Mischung der Chargen steuern. Sobald die Rohstoffe im Materialraum angeliefert werden, sind sie ständig in Bewegung.
Im Mischraum transportiert ein langes, flaches Förderband kontinuierlich Rohstoffe aus den Silos mit verschiedenen Rohstoffen schichtweise zum Becherwerk und leitet sie anschließend zur Wiegevorrichtung, um ihr Gesamtgewicht zu prüfen. Diesen Zutaten werden recycelte Glasfragmente oder Produktionsrückstände beigemischt. Jede Charge enthält etwa 10–30 % Glasbruch. Die trockenen Materialien werden in den Mischer gegeben und der Charge beigemischt. Die gemischte Charge wird vom Mischraum über das Förderband zur Lagerung in den Ofenkopfsilo befördert und anschließend vom Zuführgerät kontrolliert in den Ofen gegeben.

Typische Glaszusammensetzung
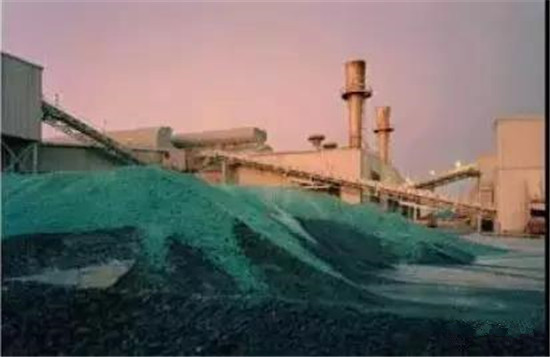
Scherbenlager
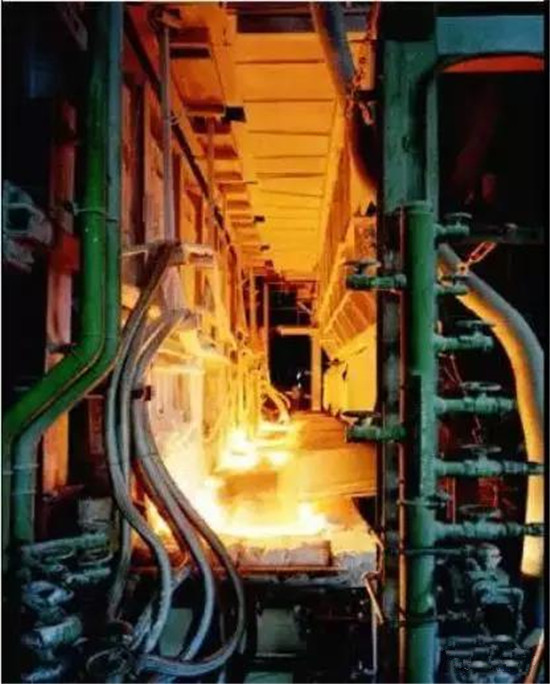
Führen Sie die gemischten Rohstoffe mit einem Trichter in den Einlass des Ofens mit bis zu 1650 Grad ein
Schmelzen
Ein typischer Ofen ist ein Querflammenofen mit sechs Regeneratoren, einer Breite von etwa 25 Metern und einer Breite von 62 Metern und einer täglichen Produktionskapazität von 500 Tonnen. Die Hauptbestandteile des Ofens sind Schmelzbad/Klärbecken, Arbeitsbecken, Regenerator und Kleinofen. Wie in Abbildung 4 dargestellt, besteht er aus speziellen feuerfesten Materialien und hat eine Stahlkonstruktion am Außenrahmen. Die Charge wird über den Zuführer in das Schmelzbad des Ofens gefördert, das mit einer Erdgas-Sprühpistole auf 1650 °C erhitzt wird.
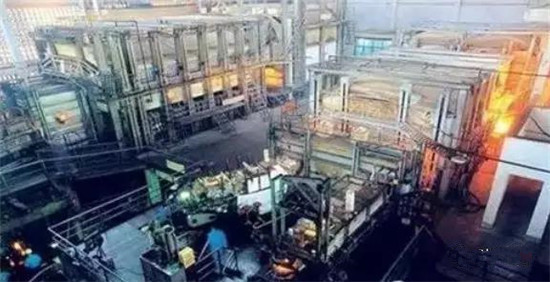
Das geschmolzene Glas fließt vom Schmelzbad durch den Klärer in den Halsbereich und wird gleichmäßig gerührt. Anschließend fließt es in den Arbeitsteil und kühlt langsam auf etwa 1100 Grad ab, um die richtige Viskosität zu erreichen, bevor es das Zinnbad erreicht.
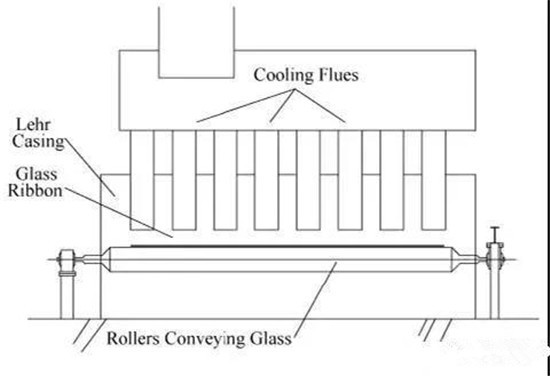
Formen und Beschichten
Die Formung des geklärten Flüssigglases zu einer Glasplatte erfolgt durch mechanische Bearbeitung entsprechend der natürlichen Materialbeschaffenheit. Die natürliche Dicke dieses Materials beträgt 6,88 mm. Das Flüssigglas fließt durch den Kanalbereich aus dem Ofen. Der Fluss wird durch eine verstellbare Tür, den sogenannten Stößel, gesteuert, die etwa ± 0,15 mm tief in das Flüssigglas eintaucht. Es schwimmt auf geschmolzenem Zinn – daher der Name Floatglas. Glas und Zinn reagieren nicht miteinander und können getrennt werden. Ihr gegenseitiger Widerstand in molekularer Form macht das Glas glatter.
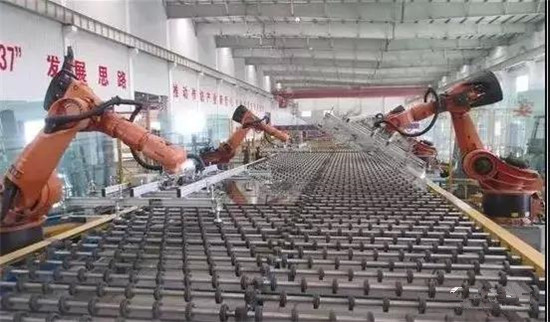
Das Bad ist eine in einer kontrollierten Stickstoff- und Wasserstoffatmosphäre abgedichtete Einheit. Es besteht aus Trägerstahl, Ober- und Unterschale, feuerfesten Materialien, Zinn und Heizelementen, einer reduzierenden Atmosphäre, Temperaturfühlern und einem computergestützten Prozessleitsystem. Es ist etwa 8 m breit und 60 m lang und die Produktionsgeschwindigkeit kann 25 m/min erreichen. Das Zinnbad enthält knapp 200 t reines Zinn bei einer Durchschnittstemperatur von 800 °C. Wenn das Glas am Ende des Zinnbadeinlasses eine dünne Schicht bildet, wird dies als Glasplatte bezeichnet und auf beiden Seiten ist eine Reihe einstellbarer Kantenzieher in Betrieb. Der Bediener verwendet ein Steuerprogramm, um die Geschwindigkeit des Glühofens und der Kantenziehmaschine einzustellen. Die Dicke der Glasplatte kann zwischen 0,55 und 25 mm liegen. Das Heizelement der oberen Trennwand wird verwendet, um die Glastemperatur zu regeln. Während die Glasplatte kontinuierlich durch das Zinnbad fließt, sinkt ihre Temperatur allmählich, wodurch das Glas flach und parallel wird. An diesem Punkt kann Acuracoat® zur Online-Beschichtung von reflektierenden Folien, Low-E-Folien, Sonnenschutzfolien, Photovoltaikfolien und selbstreinigenden Folien auf Pyrolyse-CVD-Geräten verwendet werden. Zu diesem Zeitpunkt ist das Glas zum Abkühlen bereit.
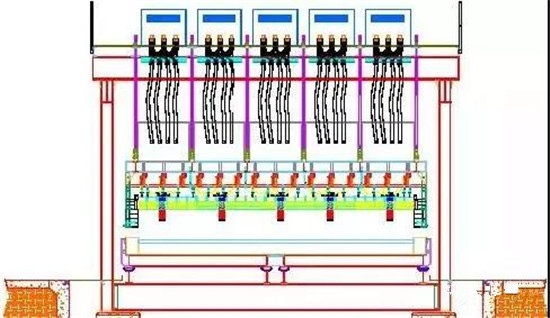
Badquerschnitt
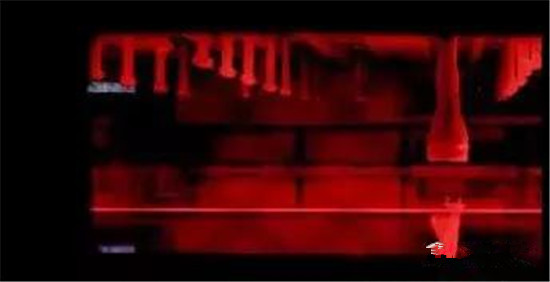
Das Glas wird in einer dünnen Schicht auf dem geschmolzenen Zinn verteilt, vom Zinn getrennt gehalten und zu einer Platte geformt
Das hängende Heizelement sorgt für die Wärmezufuhr und die Breite und Dicke des Glases werden durch die Geschwindigkeit und den Winkel des Kantenziehers gesteuert.
Glühen
Wenn das geformte Glas das Zinnbad verlässt, beträgt die Temperatur des Glases 600 °C. Wenn die Glasplatte in der Atmosphäre gekühlt wird, kühlt die Oberfläche des Glases schneller ab als das Innere des Glases, was zu einer starken Kompression der Oberfläche und schädlichen inneren Spannungen der Glasplatte führt.
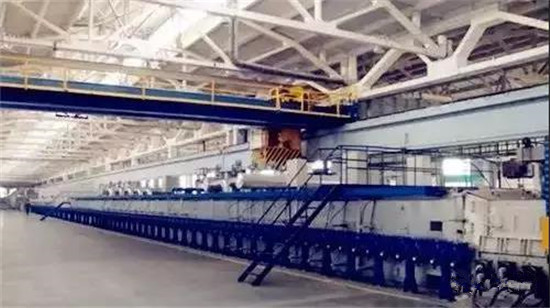
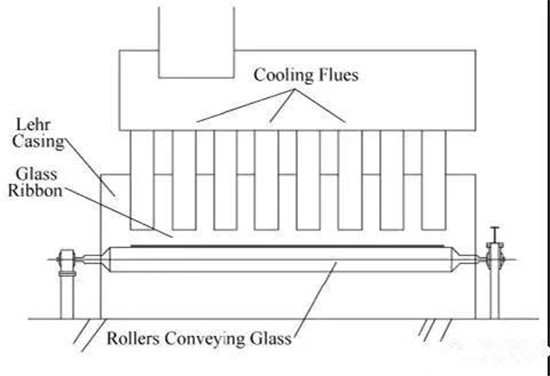
Abschnitt des Glühofens
Der Erhitzungsprozess von Glas vor und nach der Formgebung ist auch ein Prozess der inneren Spannungsbildung. Daher ist es notwendig, die Wärme zu kontrollieren, um die Glastemperatur allmählich auf Umgebungstemperatur abzusenken, d. h. zu glühen. Das Glühen erfolgt in einem Glühofen mit voreingestelltem Temperaturgradienten (siehe Abbildung 7), etwa 6 Meter breit und 120 Meter lang. Der Glühofen verfügt über elektrisch gesteuerte Heizelemente und Ventilatoren, um die Quertemperaturverteilung der Glasplatten stabil zu halten.
Das Ergebnis des Temperprozesses besteht darin, dass das Glas schonend auf Raumtemperatur abgekühlt wird, ohne dass es zu vorübergehenden Spannungen oder Beanspruchungen kommt.
Schneiden und Verpacken
Die im Kühlofen gekühlten Glasplatten werden über einen mit dem Antriebssystem des Kühlofens verbundenen Rollgang zum Schneidebereich transportiert. Das Glas durchläuft ein Online-Inspektionssystem zur Fehlerbeseitigung und wird anschließend mit einer Diamanttrennscheibe geschnitten, um die Glaskante zu entfernen (das Kantenmaterial wird als Glasbruch recycelt). Anschließend wird es auf die vom Kunden gewünschte Größe zugeschnitten. Die Glasoberfläche wird mit Pulver bestreut, damit die Glasplatten gestapelt und gelagert werden können, ohne dass sie aneinander kleben oder verkratzen. Anschließend werden die einwandfreien Glasplatten manuell oder automatisch in Stapel aufgeteilt und zur Lagerung oder zum Versand an Kunden ins Lager gebracht.
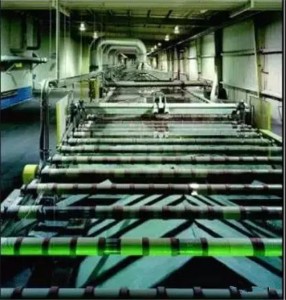
Nachdem die Glasplatte den Glühofen verlassen hat, ist die Glasplatte vollständig geformt und wird in den Kühlbereich gebracht, um die Temperatur weiter zu senken.